9205 Atmosphere Controller
<class=””>
The powerful 9205 dual-loop controller provides comprehensive, intuitive batch atmosphere furnace PID control and programming. With cHMI, the 9205 becomes a comprehensive furnace HMI for operators and maintenance personnel. By integrating with SuperDATA (or other HMI/SCADA systems), management has a comprehensive view into the performance and utilization of their equipment.
<class=””>
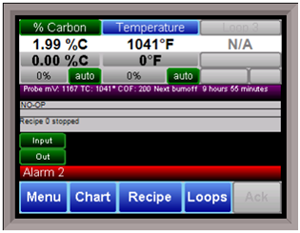
16 PIDs via program opcode |
3 PID sets/loops with defined temperature switch point |
T/C comparison with offset available for T/C checks |
Multiple alarms assigned to individual relays or a single relay |
Probe burnout & impedance test |
“0.00″ setpoint deactivates control output |
Band limits for each process variable |
Remote setpoint for third input |
Guarantee soak timer based on auxiliary load thermocouples |
Software | Description |
---|---|
TS Manager | Data management for touch screen flashcard. Remote data viewer, historical data backup, SuperDATA integration. |
Configurator | Remote setup and configuration of controller |
Load History | View historical load information. |
Control Loops | Three Loop PID controller Temperature, Temperature, Temperature Temperature and Carbon Potential Temperature and Dew Point Millivolt |
Analog Inputs | Three |
Analog Outputs | Expandable |
Digital Inputs | Four |
Digital Outputs | Eight relay outputs (Expandable to 16 or 32) |
Communication Ports | Two (2) - RS232 Three (3) - RS485 Ethernet Allen Bradley DF1 |
Display | 3.5", 5.7", 12.1", 15" and 17" Color touch screen Video recorder with "NOTES" capability Removable storage media (948 months of data) PC interface with SuperDATA |
Programmable | 300 12-Step Recipes or 300 24-Step Recipes |
Events | User-Defined |
Web Browser Enabled | Remote PC view with standard Web Browser |
Mounting | DIN rail or sub-panel mounting |
Power | 24 VDC |
This message is generated when the HMI does not have communications to the controller inside the panel. Possible reasons for this include:
Loss of 24VDC power to terminals 1 (-) and 2 (+) on the controller.
A bad communication cable between the HMI and the controller.
(Check by ringing out the cable end to end, or checking for continuity.)
Bad connection between the HMI and the controller.
(Check both ends to make sure they are securely connected and not loose or damaged.)
Cable connected to wrong port on back of HMI.
(COM1=232 and COM3=485)
SOAK is simply a specified amount of time. There are no conditions required for the timer to count down.
G_SOAK is also a soak timer, but it will only run when pre-set conditions are met and maintained. If conditions are not met, the timer is placed in hold status.
See our Schematics and Drawings Page for wiring info.
Navigate to “Slave Instrument Setup” (This may involve logging in).
Select an instrument you want to configure and tap “Edit.” Note that the list of available instruments is color coded:
Blue=atmosphere
Red=temperature
Yellow=events
White=user-selected instrument
Configure the instrument, address, and port. Note the following:
All devices on the same slave port must utilize the same protocol.
An address of zero (0) will disable the instrument.
Controllers that provide dual functions must have the same address assigned for both.
If your instrument is not shown in the list, use User Instruments 1-16 along with the Generic Instrument Setup menu (see manual for additional details).
Slave 1 = terminals 5 (-) and 6 (+)
Slave 2 = terminals 22 (+) and 23 (-)
RS-232 = 9-pin port on controller’s face
See our Instrument Setup Sheets Page for information on your device.