RGA6010
Rack-mounted and continuous Precision Measurement of Protective Heat Treating Atmospheres
CO, CO2, CH4, H2 – Used for Carburizing, FNC, and Nitriding
The rack-mounted continuous gas analyzer can be used for carburizing, neutral and ferritic nitrocarburizing heat treat applications. The measurement of the process gas provides calculated values for %C, KN, KC. In endothermic based atmospheres, the instrument in conjunction with carbon probes can be used to automatically adjust COF to provide the most precise atmosphere measurement.
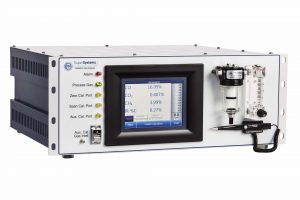
Enhances quality through process repeatability and accuracy |
On-screen trending chart |
Auto adjust mode replaces manual adjustment of COF - Probe+IR |
Sooting, air leaks, water leaks, and radiant tube leaks quickly identified through 3 gas measurement |
Auto-Calibration integrated into the MGA 6010 |
Session recording with customizable user names and equipment |
FNC and Nitriding Calculations with optional H2 Cell |
Integrated automatic calibration ports |
4-20mA output for each gas |
Two user-assigned alarm outputs with visible alarm indication |
Custom configurable calculations and gas ratios available |
Digital inputs for: Pump Start/Stop; Inhibit COF/PF adjustment; Initiate Zero calibration; Initiate Span calibration; |
IR %C calculation and indication of probe %C |
Two Ethernet ports (one direct to screen, another direct to sensor) |
Capable of Probe + IR for automatic adjustment of COF / PF |
Automatic sampling parameters prevent damage to instrument |
Color touch screen display |
Optional stainless steel transducers are required for use with non-dissociated Ammonia |
Language editor |
Data manager for downloading |
Print charts and tabular data |
Setup facility and furnace identifiers |
Add notes when capturing data |
Real time graphical display on a PC |
Export utilities |
Backup data manager |
Sampling method | Extraction by internal pump (when necessary) |
Measurement Method (CO, CO2, CH4) | Non-Dispersive Infrared (NDIR) |
Measurement Method (H2) | Thermal Conductivity |
Accuracy and repeatability | ± 1% of full scale |
Recommended Factory Calibration Interval | Annual |
Flow Meter | Front of panel and also on-screen |
AC Power Requirements | 90 to 230 VAC, 50 to 60 Hz, 60 Watts |
Communications | Ethernet, USB(A), USB(B), RS485 Modbus |
Data Storage | Continuous automatic data logging |
Data Retrieval | XGA Viewer Software (included) or on-screen |
Operating Temperature | 32° to 122° F (0° to 50° C) |
CO: Carbon Monoxide | Range: 0 - 30% |
CO2: Carbon Dioxide | Range: 0 - 2.0% Optional Range: 0 - 20.0% |
CH4: Natural Gas/Methane | Range: 0 - 20% |
Optional H2: Hydrogen | Range: 0 - 100% |
Calculated % Carbon | Range: 0.1 - 2.00% |
Suggested COF / PF factors | |
Onboard Data Acquisition | |
Enhanced with Nitriding/FNC Calculations | Carbon Potential (KC) Nitriding Potential (KN) |
COF limits predetermined for % Carbon adjustment |
Millivolt and temperature limits for furnace gas sampling |
Switch from probe + IR control to "monitor" mode |
Product Line | User Manual | Datasheet | Wiring | Other |
---|---|---|---|---|
PGA3500 | PDF | Online | |||
PGA3510 | PDF | Online | PGA 3510 Datasheet | ||
MGA 6000 | ||||
MGA 6010 | PDF | Online | MZA 6010 Datasheet | ||
RGA 6010 | PDF | Online | RGA Datasheet | ||
MZA 6010 | PDF | Online | MZA 6010 Datasheet | ||
XGA Viewer | ||||
General Info | Atmosphere Measurement and Troubleshooting |
|||
Touchscreen Cleaning Procedure | ||||
An Overview of Endothermic Generators |
If the device is used... | Then perform a calibration... |
---|---|
Daily | Weekly |
Weekly | Monthly |
Less than weekly | Prior to use |
SSi recommends 1.5 scfh. However, anywhere from 1 – 2 scfh is acceptable.
The bowl filter leading into the unit contains a filter element (p/n 37051) that can be replaced when it becomes dirty.
These are factors that go into the calculation for determining the %Carbon. Manually adjusting them will have a direct effect on the %Carbon being calculated. Contact SSi for more information.
For RS485 Communications:
- Wire to the terminals 1561 and 1571 inside the RGA.
- On the RGA screen interface, go to the Menu and log in with the number 2.
- Select “Communications and source setup” > “Atmosphere/Temp sources”
- Here you can edit to add your Probe Temp/mV Instrument or Furnace temp Instrument.
- When you have selected the appropriate device, edit the Probe Temp/mV instrument address or the Furnace temp instrument address.
To set the Device time to match the Touch screen date and time:
- Go to Menu and log in with the number 2.
- Then select “Instrument set up” > “General set up.”
- Edit the Device time to match the touch screen time by selecting “Device Time” > “Edit.”
- Call SSi at 513-772-0060 for a Code of the Day login number.
- Log in with the code.
- Select the “Factory use only” option.
- On the following screen select “Set Instrument Type.”
- Set the Nitrider Calculations option to Enable.
- You will then need to cycle power to have the correct Calculations page displayed.
The MGA displays a calculated dew point using gas values and requires assumptions regarding the composition of the gas being sampled. Since these assumptions are not always accurate, the resulting dew point is not always accurate.
- First, make sure you have the Zero and Span gas tanks hooked up to the correct calibration ports on the side of the RGA.
- On the Interface go to Menu and log in with the number 2.
- Select “Automatic Calibration setup.” You will see the options to set the Auto calibration to YES or NO.
- Select “YES” to set up your desired calibration purge and intervals.
SSi recommends that the RGA be mounted fairly close to the source it is sampling. It can be further away, but a longer sample tube increases the likelihood of leaks or contaminants.
The incoming pressurized gas goes through a small fixed orifice inside the analyzer, which should require between 20 and 50 psi to maintain proper flow.
- Go to the Menu and log in with the number 2.
- Select “Automatic Calibration set up” then change the Auto Calibration from YES to NO. That will clear the Auto Calibration alarm banner.
**It is important to note WHY you were getting the alarm, to make sure that you were getting adequate flow and the calibration was able to complete successfully.